The weave is completed with a High Density Polyethylene base. High
Density Polyethylene is structured as a poly in a way that gives a
two-directional strength. Often, grocery store bags are manufactured
using a High Density Polyethylene poly for the purpose of holding
greater weight and not breaking through the bottom of the bag. This
allows for a strong single directional plane with High Density
Polyethylene. The weakness of this type of poly lies in the opposite
directional plane. The High Density Polyethylene can easily tear (like
paper) on the other directional plane. The weave in packaging allows for
a strong resistance to tearing from multiple directions as opposed to
an extruded sheeting. As the High Density Polyethylene weave creates a
mesh of opposing strengths in the structure. This allows greater
resistance to tears in the wind or staples ripping through when
packaging.
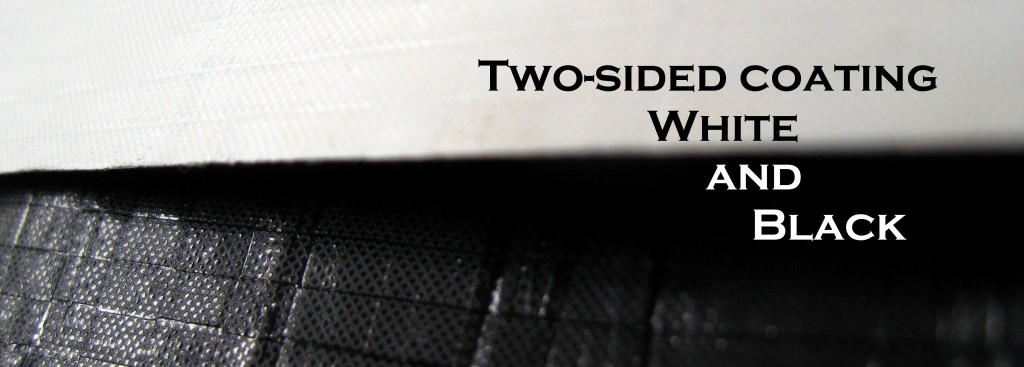
The High Density Polyethylene weave is coated on both sides with a
Low Density Polyethylene. Low Density Polyethylene is known to have more
stretch than High Density Polyethylene. While High Density Polyethylene
will either hold or break, Low Density Polyethylene will hold, stretch,
and then eventually break.
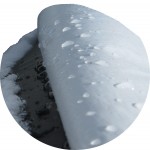
When the two types of poly are combined, the product becomes
useful in packaging design by allowing for a strong industrial fabric.
The mixture of the weave and coating creates a water resistant and tear
resistant plastic, which is perfect for industries shipping by rail and
truck.
Please feel free to contact Flexpak at any point to request more
information about what type of plastic can be used in the manufacturing
of a pallet cover for your specific product.